1. Green sand casting
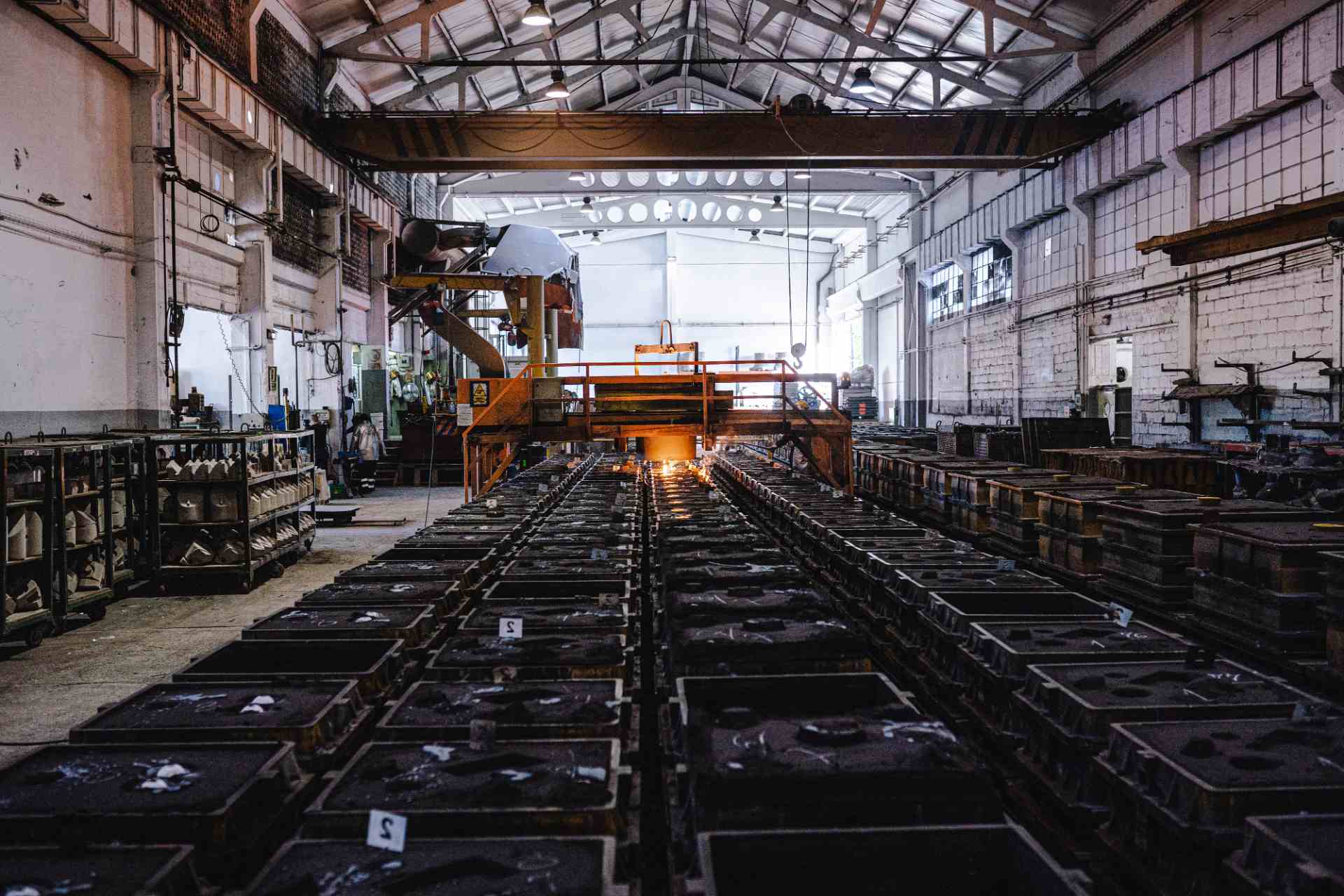
A greensand casting is created in an uncured sand mould bonded with clay. The term refers to the fact that the mould is uncured rather than the colour of the sand. Dry-sand moulds are similar, but the sand is baked before being filled with metal. Alternatively, sodium silicate can be mixed into the sand to form chemical linkages that eliminate the need for baking. Molds built of coarse loam sand, backed up with brick, and faced with extremely refractory material are used for heavy castings.
2. Sand preparation
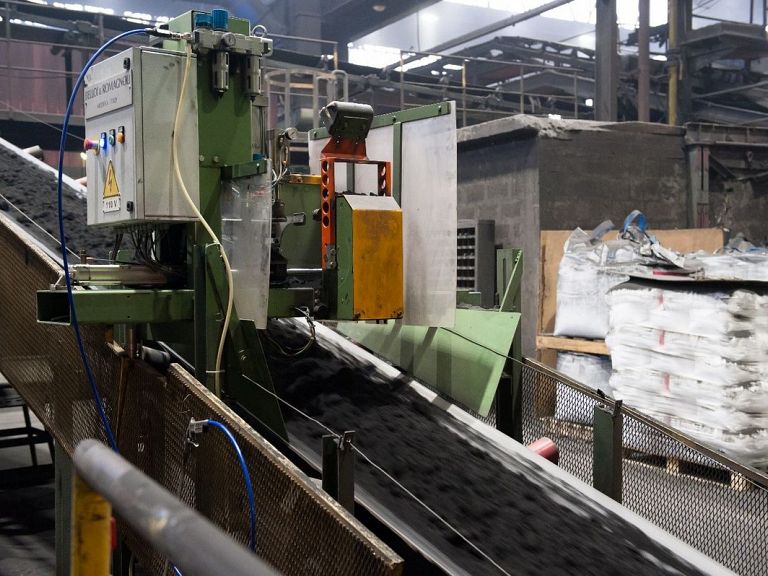
Prepare sand and core sand for moulding by mixing used sand with the appropriate amount of clay in a sand mixer. Molds and core boxes are built in accordance with the part designs. For single-part manufacturing, we can utilise wooden moulds, plastic or metal moulds for mass production, and pattern plates for massive castings. Molds are now manufactured by engraving machines, which considerably shortens the production cycle, which can take 2 to 10 days.
3. Molding
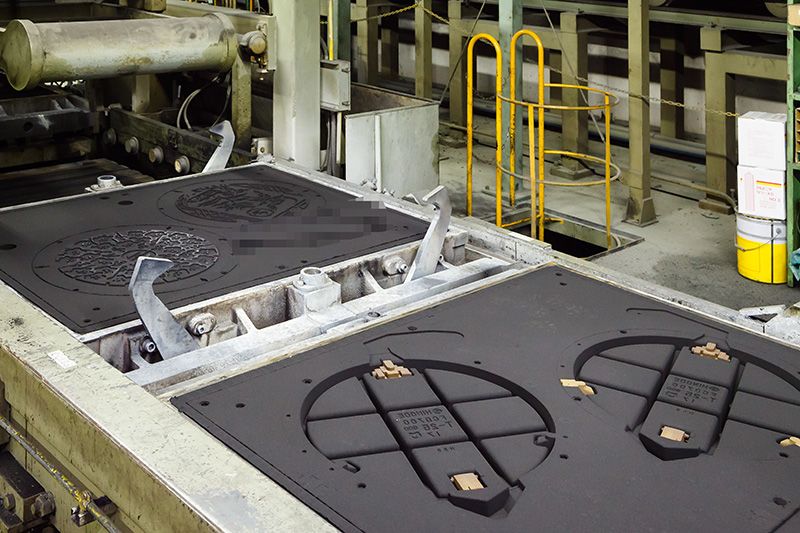
Sand moulding includes sand moulding, core fabrication, and mould fitting. Sand moulding is the process of creating a hollow for a casting out of moulding sand. The creation of cores, which are utilised to construct the interior shape of the casting, is referred to as core making. The assembling of the top and lower sandboxes after the cores have been inserted into the cavity is known as mould fitting. Molding is an important step in the casting process.
4. Melting
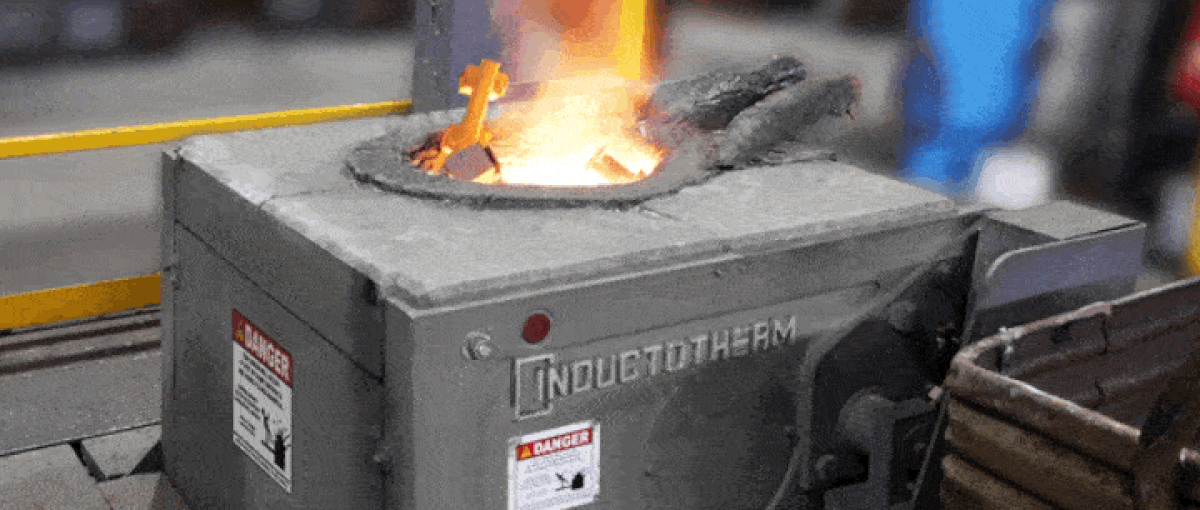
The chemical composition must be compatible with the desired metal. The alloy material is melted in a suitable furnace to generate a certified liquid metal (piece and temperature of the molten metal must comply). Cupolas or electric furnaces are used in melting (due to environmental requirements, cupolas have mainly been outlawed, so electric furnaces are the primary choice).
5. Pouring

A ladle is used to pour molten metal from the electric furnace into the mould. Pouring speed is crucial to guarantee that the molten iron fills the whole cavity. Pouring the iron is equally dangerous, so use caution!
6. Fetling
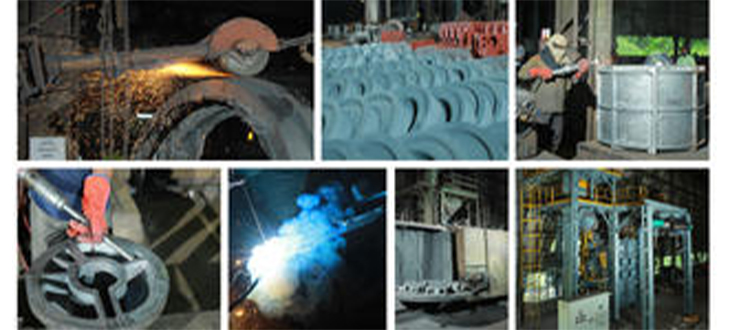
Nexus Cast has a strategy in place to carry castings from the mould dumper to the primary shot blasting point via a conveyor. Following the initial shot blasting, the castings would be shipped grinding. Shot blasting is simply a cleaning procedure in which abrasive material is pushed via a jet nozzle utilising compressed air to impact on the casting surfaces. Fettling is critical for final castings to guarantee that the pieces fulfill aesthetic and dimensional criteria. At Nexus Cast, fettling machinery such as hangar type and wire mesh type machines are installed. Manual grinding on conventional grinding equipment is another finishing procedure used at Nexus Cast to finish castings.
7. Coating
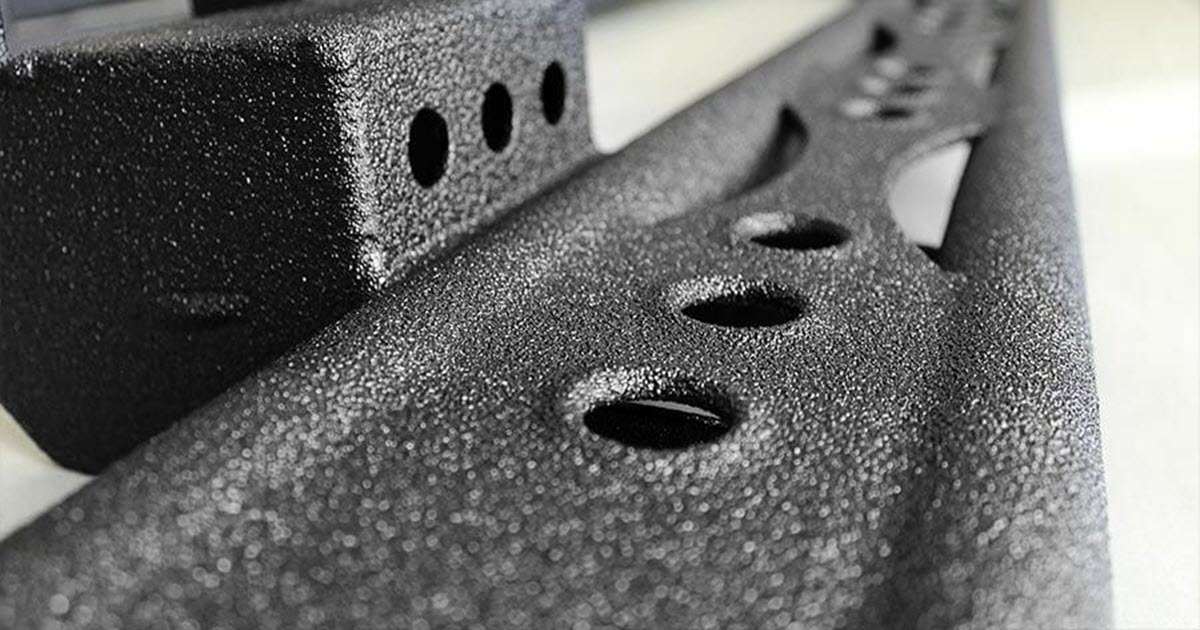
Casting coating is a significant casting raw and auxiliary material that plays a vital role in assuring the surface quality of castings. Many factors influence the technical features of casting coating. The major technical indicators of casting coating have a significant impact on casting quality. The essential conditions for ensuring that coatings play a role are the right purchasing and application of coatings. High efficiency, environmental protection, and economics will be major future paths for paint development.New moulding processes, such as lost foam and V-process, necessitate the creation of matching coatings. The rising demand for casting quality necessitates the development of the matching casting coating. The casting coating has the finest development prospects.
8. Packing
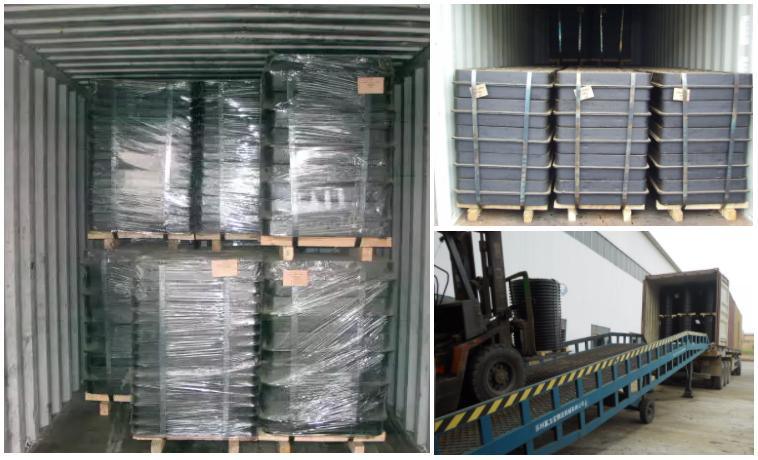
There are several packing options available, which are chosen based on the type of goods and the amount of the order. Once the appropriate design dimensions and handling limits are determined, the optimal packing and shipping techniques are specified for each new product. Special packaging is frequently required to meet individual units or bulk packing needs. Custom packing is another alternative for meeting the client's individual needs or designing specialised solutions for domestic or international shipments.